The Watchmen Part 2: Power Management
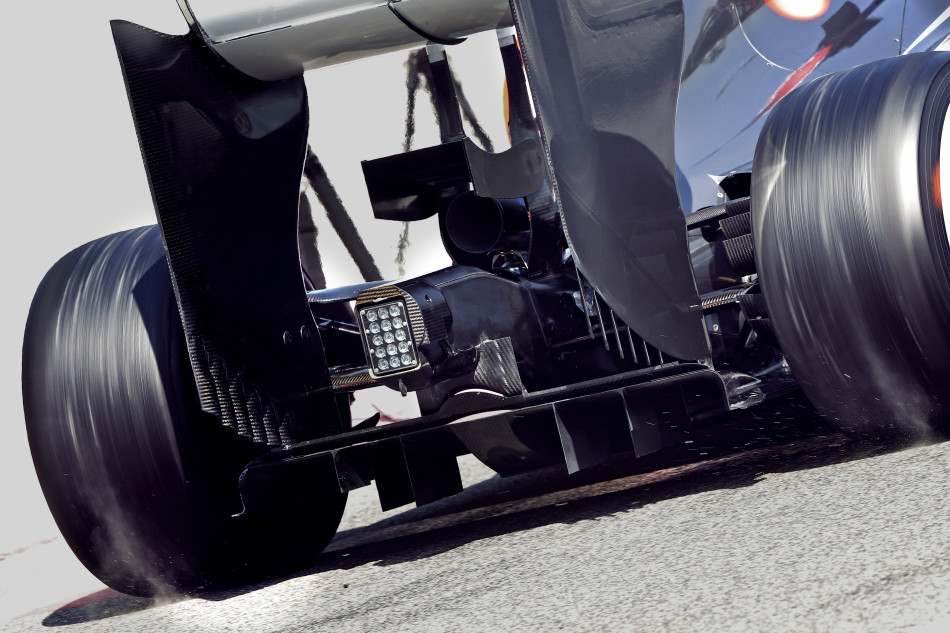
Until this year, Formula One had been faithfully wedded to powerplant technology that had it roots in an age where access to the power required for F1 meant large capacity engines burning fuel with abandon.
But as the world woke up to the need to conserve resources and to develop technologies to do so and as automobile manufacturers pressed for change, Formula One too realised that it had a role to play in developing these technologies
As such, the old 2.4 litre, eight-cylinder, normally-aspirated engines that F1 had relied on since 2006 were phased out and manufacturers were handed a engineering challenge the like of which the sport had never seen.
The task was to develop to a small 1.6 litre, six cylinder internal combustion engine which would work in harmony with two radical new energy recovery systems that would boost its power. The first, a vastly expanded kinetic energy recover system of the sort used since 2009 now called ERS-K and a second system ERS-H, a system attached to a new turbocharger which would recover energy from exhaust gasses.
The new Power Units are a marvel, generating as much or more power than the fuel-hungry old V8s, but from 35 per cent less fuel than previously used.
They are incredibly complex, however, and making sure that the new systems meet the requirements of F1’s technical regulations is a far trickier task than with the engines of old.
A known quantity, the V8s, the technical specifation of which had been frozen in 2007, provided teams with little room for manoeuvre, as FIA software analyst Olivier Hulot admits: “It was settled. It had been around for years, so the software inside the standard ECU (engine control unit) was the same for everyone. You could play with a few parameters for control of the V8, but that was it.”
Fast-forward to 2014 and the game has changed, with the high-tech systems requiring a huge rethink of the standard ECU brought to the sport by the FIA in 2008.
“Prior to this year all the control software, everything that was managing the engine – the gearbox, differential, clutch and so on – was standard code. The teams had no ability to change that code,” says Alan Prudom, who heads up the FIA software analysis team at the races. “This year the teams have been given more freedom, in that they are able to write some of their own code. It is still within the same standard ECU as last year, but there are some areas we’ve set aside for which the teams can write code. That’s primarily for things like the management of energy recovery systems, the way the energy is balanced around the unit. They can have an influence on choosing strategies for the way in which engine power is delivered, what proportion is from the internal combustion engine and what comes from the battery and the associated motors.
“There’s also a fair amount of freedom on some of the newer technologies such as the turbo management. However, most of the chassis side of things like the gearbox control and clutch differential is still standard software that the teams can only configure, they can’t actually change it.”
These advances mean that whereas before analysis of a team’s use of the ECU was relatively straightforward, this year the FIA technical team must sift through a vast amount of code to ensure teams are conforming to the rules.
"A lot of the work we do for a grand prix is preparation, it’s before the race weekend,” explains Hulot, who is responsible for ECU checks. “Pre-season we visit all the teams, all the engine suppliers and check how they’re connecting the standard ECU to their car systems.
“Then before each race we look at how they configure the standard parameters, making sure this is in compliance with the regulations. Before each session we verify again the configuration of the standard issue.”
And the analysis doesn’t stop there. During each session the FIA’s software analysts have access to live data from the cars, which they look at throughout the weekend, searching for signs of untoward performance.
“We have dashboard-type displays that give us warnings when somebody is running close to the limit in terms of a specific regulation,” explains Hulot. “Largely it’s an exercise in trying to minimise post-event analysis, because after the event it’s too late.”
Allied to analysis of the ECU is an examination of the control units of the new energy recovery systems themselves, a task managed by Andy Leitch.
“The kinetic energy recovery is basically the same as the old KERS– you have the same control electronics going between the battery and the motor. But then it’s doubled up. You’ve got a second motor generator unit on the turbo and also the size of the motors has increased. So instead of 60kW it’s now 120kW,” he says.
“In terms of what we’ll be looking for, there are limits on how much power the kinetic recovery motor generator (MGU-K), can provide. There are also limits on how much energy can be taken in and out of the battery. From a safety point of view we’ve put a maximum voltage of a thousand volts to be used, so we’re making sure the teams don’t exceed that, which they shouldn’t do by design. There’s also a maximum speed permitted for the turbo motor.”
Again the analysis is a mix of pre-race checks and data examination performed in real time.
“The weight of the battery is defined so a team can’t have a really light battery that’s got high capacity. There’s no point in them spending a lot of money trying to get a special battery made that’s going to be a bit lighter because it won’t help – you’ll end up having to put ballast on [the car] to compensate,” he adds. “Those design elements are checked before the start of the season.
“On the car itself we have two sensors: one for the MGU-K and one in the battery to measure how much energy goes in. During running we’re looking at those to see how much energy, how much power, how much voltage is present. And if our sensor fails the teams have to provide a model of the power they’re using, which I can then verify.”
All these systems are also locked, either by physical or software seals, so that the teams are prevented from making adjustments.
Prudom admits that the complexity of the new units has increased the responsibilities of the FIA’s software team, with an extra software analyst taken on to help shoulder the burden. “I’ve been working in this area of Formula One for 20 years and these are by far the most complicated engines I’ve dealt with – by a factor of two or three,” he says. “They are a far more extreme design than, say, the previous V8s were. So it is extra work for sure and I think everyone, the teams and ourselves, is on a learning curve with them.”
And the learning curve has been steep. Pre-season testing saw every powerplant manufacturer suffer reliability issues, with Renault the worst affected. Despite the difficulties, however, each manufacturer was bound by the new rules to homologate its power unit on February 28th.
“This work was undertaken by our engine expert John Marson,” says Bauer. “Each team must submit a reference power unit that we can check against whatever they’re doing during the year. Basically, it’s the closing of the boxes, so to speak. After that point the only option for the manufacturers to alter the power units is on the grounds of reliability, safety or cost, and that request must then be submitted to the FIA for approval. John also looks after power unit checks at the races, making sure that the right components are being used, as the teams are restricted on the number of certain elements they can use.”